Essential Pole Line Hardware for Modern Grids
Pole Line Hardware forms the backbone of overhead power transmission and distribution, as well as telecommunication networks. These critical components, though often unseen, are indispensable for the safe, reliable, and efficient delivery of electricity and data. From bustling urban centers to remote rural landscapes, overhead pole line hardware ensures that communities remain connected and powered. As technology evolves and the demand for uninterrupted service grows, the significance of high-quality, durable electrical pole line hardware and telecommunication pole line hardware cannot be overstated. This comprehensive guide will delve into the various facets of pole line hardware, its applications, key components, and the importance of selecting a trusted supplier like EPCOM for these essential elements.
Understanding Pole Line Hardware and Its Importance
At its core, pole line hardware encompasses a wide array of metallic and non-metallic components used to construct and maintain overhead utility lines. These lines can be for electrical power, telephone services, or fiber optic communications. The hardware serves multiple functions, including supporting conductors, providing insulation, terminating lines, and ensuring the structural integrity of the entire pole-mounted system. Without robust utility pole line hardware, the infrastructure would be susceptible to failure from environmental stresses like wind, ice, and temperature fluctuations, as well as mechanical loads.
The reliability of our power grids and communication networks is directly tied to the quality and proper installation of every piece of pole line hardware. A single faulty component can lead to cascading failures, resulting in costly outages, safety hazards, and significant disruptions. Therefore, investing in superior pole line hardware components is not merely a technical requirement but a crucial decision for long-term operational excellence and public safety.
What Constitutes Pole Line Hardware?
Pole line hardware is a broad category that includes a multitude of items, each designed for specific functions. These components work synergistically to create a functional and resilient overhead system. Some of the primary categories within types of pole line hardware include:
- Anchoring and Guying Components: These are vital for stabilizing poles and counteracting the forces exerted by conductors and environmental factors. This category includes items such as guy wires, anchors, stay rods, and associated fittings.
- Conductor Support Hardware: This group involves clamps, brackets, and crossarms that physically hold the conductors (wires or cables) in place on the pole.
- Insulators: Essential for electrical systems, insulators prevent the flow of current from the energized conductors to the pole or other structures, ensuring safety and preventing power loss.
- Connectors and Terminating Hardware: Used to join sections of conductors or to terminate them at specific points.
- Fasteners and Brackets: A wide variety of bolts, nuts, washers, screws, and specialized brackets used to assemble and secure all other hardware components to the pole and to each other.
- Pole Protection and Reinforcement: Items like pole steps, pole bands, and ground wire moulding that enhance the safety, accessibility, and longevity of the pole itself.
EPCOM specializes in providing a comprehensive range of these components, ensuring that every aspect of your overhead line construction and maintenance needs is covered with high-quality solutions.
The Critical Role of Quality Pole Line Hardware in Infrastructure
The infrastructure for power distribution and telecommunications is foundational to modern society. The performance and longevity of this infrastructure heavily depend on the quality of the pole line hardware used. High-quality hardware offers several key benefits:
- Enhanced Reliability: Superior materials and manufacturing processes result in hardware that can withstand harsh environmental conditions and mechanical stresses, reducing the likelihood of failures and outages. This is paramount for pole line hardware for power distribution.
- Increased Safety: Properly designed and manufactured pole line hardware minimizes risks such as falling lines, pole collapse, or electrical faults, protecting both utility workers and the general public.
- Extended Service Life: Durable hardware, resistant to corrosion and wear, means fewer replacements and lower maintenance costs over the lifespan of the utility line. This is a key consideration when sourcing durable pole line hardware.
- Optimal Performance: Efficient conductor support, secure connections, and effective insulation contribute to the optimal performance of the electrical or communication system, minimizing losses and ensuring signal integrity.
- Cost-Effectiveness: While high-quality hardware might have a slightly higher upfront cost, its longevity and reliability translate into significant long-term savings through reduced maintenance, fewer repairs, and minimized downtime.
Choosing a reputable pole line hardware supplier like EPCOM ensures access to components that meet stringent quality standards, contributing to a more robust and dependable infrastructure. For more information on industry standards, organizations like the IEEE (Institute of Electrical and Electronics Engineers) provide valuable resources.
Key Components in Pole Line Hardware Systems from EPCOM
EPCOM is committed to providing a wide array of essential pole line hardware components designed for durability and performance. Among these, stay assemblies play a crucial role in maintaining the stability and integrity of utility poles. Let’s explore some of these vital products offered by EPCOM.
Anchoring and Support: The Crucial Role of Stay Assemblies
Stay assemblies, also known as guy assemblies, are fundamental to the stability of utility poles, especially those subjected to lateral forces from conductors, wind, or changes in line direction. These assemblies counteract such forces, keeping poles upright and lines secure. Effective stay assemblies are a cornerstone of reliable overhead pole line hardware. EPCOM offers a complete suite of components for robust stay assemblies.
Stay Wire: The Tensile Strength of Your Pole Line
The Stay Wire, often called guy wire, is a high-tensile steel cable that forms the primary tension element in a stay assembly. It runs from the upper part of the pole to an anchor point in the ground. The quality of the stay wire is paramount, as it must withstand continuous tension and varying environmental conditions. EPCOM’s Stay Wires are manufactured to meet rigorous standards, ensuring excellent tensile strength, corrosion resistance, and longevity. They are available in various grades and sizes to suit different load requirements and environmental challenges, making them a critical part of any pole line hardware installation.
Proper selection of stay wire diameter and material (e.g., galvanized steel for corrosion protection) is crucial. The galvanization process, typically hot-dip galvanizing, provides a thick, durable zinc coating that protects the underlying steel from rust and degradation, significantly extending the service life of this essential pole line hardware accessory.
Stay Rod: Connecting Strength to Ground
The Stay Rod, also known as an anchor rod, provides the vital connection between the stay wire and the ground anchor. It transmits the tensile forces from the stay wire to the earth. Stay rods must possess high tensile strength and excellent corrosion resistance, as a significant portion of the rod is often buried. EPCOM’s Stay Rods are engineered for maximum durability, often featuring hot-dip galvanization for superior protection against soil-induced corrosion. They come in various lengths and diameters, with options for different eye types (e.g., thimble eye, oval eye) or forged eyes to securely attach the stay wire. The choice of stay rod depends on factors like soil conditions, load requirements, and the type of anchor being used. These are indispensable pole line hardware components for any robust guying solution.
Installation of stay rods requires careful consideration of the angle and depth to ensure optimal holding power. The interface between the stay rod and the anchor (such as an expanding anchor or a rock anchor) is critical for the overall stability of the pole structure.
Stay Thimble: Protecting the Wire, Ensuring Longevity
To protect the stay wire from wear and deformation at the point of connection, a Stay Thimble is used. This grooved metal fitting is inserted into the loop of the stay wire where it connects to the eye of a stay rod, insulator, or other hardware. The thimble provides a smooth, rounded surface for the wire to bend around, preventing kinking and reducing stress concentration, which could otherwise lead to premature wire failure. EPCOM offers Stay Thimbles made from durable materials, often galvanized steel, to ensure they withstand the compressive forces and environmental exposure. They are an essential, albeit small, piece of high-quality pole line hardware that significantly contributes to the lifespan of the stay assembly.
Stay thimbles come in different sizes to match the diameter of the stay wire being used. Ensuring a proper fit is important for the thimble to function effectively. Heavy-duty thimbles are available for applications with higher loads or more aggressive environmental conditions.
Stay Plate: Distributing Load for Secure Anchoring
The Stay Plate, sometimes referred to as an anchor plate or bearing plate, is used in conjunction with stay rods and anchors, particularly with certain types of ground anchors like plate anchors. It serves to distribute the load from the stay rod over a wider area of soil, increasing the holding capacity of the anchor system. This is especially important in softer soil conditions where a concentrated load could lead to anchor pull-out. EPCOM’s Stay Plates are robustly constructed, typically from steel, and are often galvanized for corrosion resistance. Their design ensures effective load distribution, contributing significantly to the stability offered by the utility pole line hardware‘s anchoring system.
The size and thickness of the stay plate are determined by the expected load and the soil’s bearing capacity. In some designs, stay plates might have ribs or other features to enhance their grip in the soil and prevent rotation.
Insulation in Pole Line Hardware Solutions: Safety and Efficiency
Insulation is a non-negotiable aspect of electrical pole line hardware. Insulators prevent the electrical current from flowing from the live conductors to the pole (which could be conductive if metallic or wet if wooden) or to the guy wires. This ensures safety for personnel and the public, prevents power leakage, and maintains system efficiency. Various types of insulators are used in pole line construction, depending on voltage levels, environmental conditions, and mechanical loads.
Stay Insulator: Isolating Guy Wires Effectively
While stay wires are essential for structural support, they can become inadvertently energized if they come into contact with live conductors or through electrical faults. To mitigate this hazard, a Stay Insulator (also known as a guy strain insulator) is installed in the stay wire. This insulator breaks the electrical continuity of the stay wire, ensuring that the lower portion, accessible from the ground, remains de-energized even if the upper portion becomes live. EPCOM’s Stay Insulators are typically made from high-strength porcelain or polymeric materials, offering excellent dielectric properties and mechanical strength. They are designed to withstand both the tensile load of the stay wire and the electrical stresses. This is a critical safety component within the pole line hardware system.
Stay insulators are generally egg-shaped or cylindrical and are designed so that if the insulating material fails mechanically, the guy wire loops will interconnect, maintaining the mechanical integrity of the guy, albeit without insulation. This “fail-safe” design is a key feature. The selection of a stay insulator depends on the voltage of the power line and the mechanical strength required for the guy assembly.
Other Essential Components for Robust Networks
Beyond stay assemblies and insulators, a multitude of other components are critical for building and maintaining overhead lines. These include:
- Crossarms: Horizontal members attached to the pole, typically made of wood, steel, or composite materials, that support insulators and conductors. The choice of crossarm depends on the number of conductors, their spacing, and the mechanical load.
- Pole Bands and Clamps: Used for attaching crossarms, guy wires, and other equipment to the pole. Various designs exist for different pole types (wood, concrete, steel) and applications.
- Conductor Clamps: These include suspension clamps (allowing conductor movement) and dead-end clamps (terminating conductors and transferring their tension to the pole structure via insulators). Material compatibility with the conductor (e.g., aluminum clamps for aluminum conductors) is crucial to prevent galvanic corrosion.
- Grounding Hardware: Components like ground rods, ground wire, and connectors are essential for system and personnel safety, providing a path for fault currents to dissipate into the earth.
- Fasteners: A wide variety of bolts (e.g., machine bolts, double arming bolts, eye bolts), nuts, washers, and lag screws specifically designed for pole line hardware applications. These fasteners are often hot-dip galvanized for corrosion resistance.
- Wildlife Protectors: Devices designed to prevent birds and other animals from making contact with energized components, which can cause outages and harm wildlife.
Each of these components, while seemingly small, plays a vital role in the overall integrity and functionality of the pole line hardware system. EPCOM understands the importance of each part and strives to provide comprehensive, high-quality solutions.
Applications: Powering and Connecting the World
The applications of pole line hardware are extensive, primarily centered around the infrastructure for electricity and communications. The robustness and reliability of these services depend directly on the quality of the hardware used in their overhead networks.
Pole Line Hardware in Power Transmission and Distribution
This is arguably the most critical application of pole line hardware. From high-voltage transmission lines that carry bulk power over long distances to medium and low-voltage distribution lines that deliver electricity to end-users, electrical pole line hardware is indispensable.
- Transmission Lines: While many high-voltage transmission lines use large steel towers, some transmission and sub-transmission lines utilize pole structures, especially in challenging terrain or for specific voltage classes. The hardware used must withstand very high mechanical and electrical stresses.
- Distribution Networks: This is where the majority of pole line hardware is found. Distribution lines, typically operating at voltages from a few kilovolts up to 35kV (or higher in some regions), crisscross urban and rural areas. Components like crossarms, insulators, conductor clamps, transformers, and protective devices are all mounted on poles using various types of hardware.
- Rural Electrification: Pole line hardware is fundamental to extending electricity grids to remote and underserved areas. Cost-effective and durable hardware solutions are essential for the economic viability of such projects.
- Street Lighting: Many street lighting systems are pole-mounted and require specialized hardware for fixture attachment and wiring.
The demands on pole line hardware for power distribution are significant, including constant tension from conductors, dynamic loads from wind and ice, temperature variations, and the need for high dielectric strength in insulators. EPCOM’s products are designed to meet these demanding conditions.
Telecommunication Uses of Pole Line Hardware
While fiber optics are increasingly being run underground, aerial deployment on poles remains a common and cost-effective method, especially for extending networks or in areas where trenching is difficult. Telecommunication pole line hardware shares many similarities with electrical hardware but also has unique requirements.
- Telephone Lines: Traditional copper telephone lines have long been supported by pole infrastructure using specific types of wires, insulators (though at much lower voltages), and suspension hardware.
- Cable Television (CATV): Coaxial cables for CATV are often strung on utility poles, requiring appropriate clamps, lashing wires, and support hardware that can handle the cable’s weight and diameter.
- Fiber Optic Cables (FOC): Aerial fiber optic deployment uses specialized pole line hardware designed to protect the relatively delicate fiber optic cables. This includes clamps that avoid excessive pressure, snowshoes or storage loops for managing slack, and tangent supports. Due to the light weight of FOC, the mechanical load requirements might be different from heavy electrical conductors, but proper sag and tension management are still critical.
- Wireless Communication Antennas: Poles often serve as mounting structures for small cell antennas, Wi-Fi access points, and other wireless communication equipment, requiring specific brackets and mounting hardware.
For telecommunication applications, particularly fiber optics, ensuring minimal signal loss and protecting the cables from damage are key considerations. The pole line hardware must provide stable support without inducing stress points or micro-bends in the optical fibers. Information on telecommunication infrastructure can often be found via resources like the Telecommunications Act of 1996 which spurred much development.
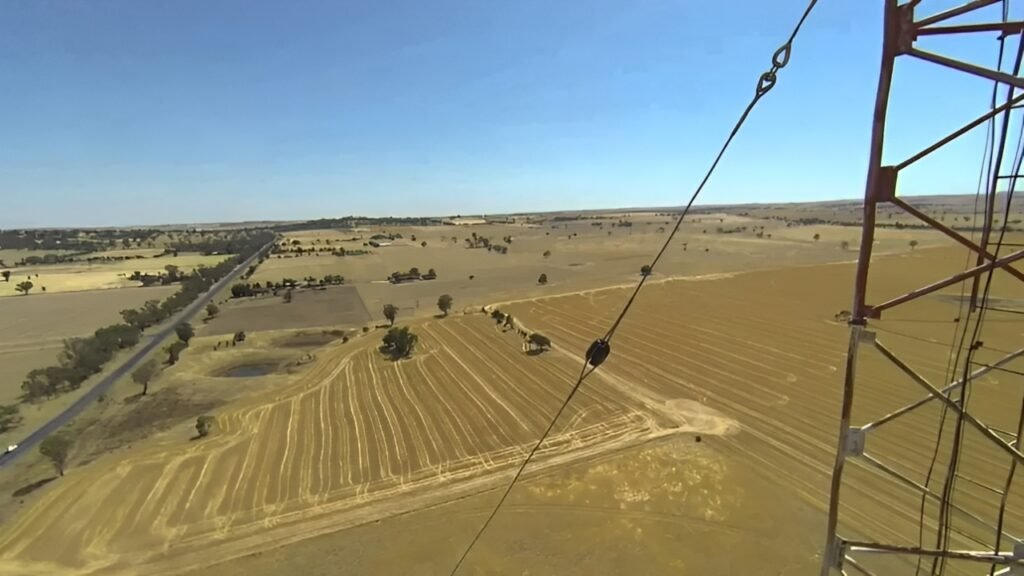
Choosing the Right Pole Line Hardware Supplier: Why EPCOM Stands Out
Selecting a supplier for pole line hardware is a critical decision that impacts the reliability, safety, and cost-effectiveness of your overhead line projects. The market has numerous pole line hardware suppliers, but not all offer the same level of quality, expertise, or service. EPCOM is dedicated to being a leader in this field.
Factors to Consider When Selecting Pole Line Hardware
When evaluating potential suppliers for your pole line hardware needs, several key factors should be considered:
- Product Quality and Compliance: Does the hardware meet relevant industry standards (e.g., ANSI, IEC, IEEE, RUS)? Are materials certified, and are manufacturing processes robust? Look for suppliers who emphasize quality control and material traceability.
- Range of Products: A supplier offering a comprehensive range of pole line hardware components can simplify procurement and ensure compatibility between different parts of your assembly. This includes everything from fasteners to specialized clamps and insulators.
- Material Specifications and Durability: Understand the materials used (e.g., ductile iron, forged steel, aluminum alloys, porcelain, polymers) and their suitability for your specific environmental conditions (corrosion, UV exposure, temperature extremes). Hot-dip galvanization is a common requirement for steel components.
- Technical Expertise and Support: Can the supplier provide technical assistance, including advice on product selection, application guidelines, and custom solutions if needed? Experienced staff can be invaluable.
- Manufacturing Capabilities: For custom pole line hardware or specific modifications, a supplier with strong in-house or partnered manufacturing capabilities is advantageous.
- Supply Chain and Availability: Reliable delivery schedules and adequate stock levels are crucial to keep projects on track. Inquire about lead times and inventory management.
- Reputation and Experience: Look for suppliers with a proven track record in the industry. Customer testimonials, case studies, and years of operation can be good indicators.
- Price and Value: While cost is always a factor, the lowest price may not represent the best value. Consider the total cost of ownership, including longevity, maintenance, and the potential costs of failure.
EPCOM’s Commitment to Quality and Durability
At EPCOM, we understand the critical nature of pole line hardware. Our commitment is to provide our customers with products that not only meet but exceed their expectations for quality, durability, and performance. Here’s how EPCOM differentiates itself:
- Stringent Quality Control: We implement rigorous quality control measures at every stage, from raw material sourcing to final product inspection. Our high-quality pole line hardware is designed and manufactured to comply with relevant international standards.
- Premium Materials: We utilize high-grade materials selected for their strength, corrosion resistance, and longevity in demanding field conditions. This includes appropriately specified steels, aluminum alloys, and insulating materials.
- Advanced Manufacturing Techniques: EPCOM leverages modern manufacturing processes to ensure precision, consistency, and optimal mechanical properties in all our pole line hardware components.
- Comprehensive Product Portfolio: We offer an extensive range of pole line hardware, including the featured Stay Wire, Stay Rod, Stay Thimble, Stay Plate, and Stay Insulator, alongside many other essentials.
- Customer-Centric Approach: EPCOM works closely with customers to understand their specific needs and challenges, offering tailored solutions and responsive support. We aim to be more than just a supplier; we strive to be a reliable partner in your projects.
- Focus on Innovation: We continuously monitor industry advancements and material science to ensure our product offerings, including durable pole line hardware, incorporate the latest improvements for enhanced performance and lifespan.
Choosing EPCOM means investing in the reliability and longevity of your overhead infrastructure. We are dedicated to powering and connecting communities with superior pole line hardware solutions.
Installation and Maintenance
The performance and lifespan of pole line hardware are not solely dependent on its inherent quality but also significantly on proper installation and diligent maintenance. Adhering to best practices in these areas is crucial for ensuring the safety, reliability, and longevity of overhead utility lines.
Best Practices for Pole Line Hardwares Installation
Correct installation is the foundation of a durable and safe overhead line system. Even the highest quality pole line hardware can fail prematurely if not installed correctly. Key best practices include:
- Adherence to Design Specifications: Always install hardware according to the engineering design and manufacturer’s recommendations. This includes correct positioning, orientation, and spacing of components.
- Proper Torque Values: Fasteners like bolts and nuts must be tightened to the specified torque values. Under-tightening can lead to loose connections and wear, while over-tightening can stress components or damage threads. Torque wrenches should be used for critical connections.
- Correct Conductor Handling: Conductors should be handled carefully to avoid kinking, abrasion, or other damage. Clamps must be appropriate for the conductor type and size to ensure a secure grip without damaging the strands.
- Appropriate Sag and Tension: Conductors and stay wires must be sagged to the correct tension according to sag charts, considering temperature, span length, and ice/wind loading conditions. Improper tension can lead to excessive stress on hardware or excessive sag.
- Secure Anchoring: Stay assemblies must be anchored securely. The type of anchor and installation method should be appropriate for the soil conditions and expected load. The angle of the stay wire is also critical for effective support.
- Insulator Care: Insulators, especially porcelain, should be handled carefully to avoid chipping or cracking. Ensure they are clean before installation.
- Grounding Integrity: All grounding components must be installed correctly to ensure a continuous, low-resistance path to earth. Connections should be tight and protected from corrosion.
- Qualified Personnel: Pole line hardware installation should always be carried out by trained and qualified lineworkers who understand the equipment, safety procedures, and construction standards. The Occupational Safety and Health Administration (OSHA) provides regulations and guidelines for electrical power work.
- Site Preparation and Safety: Ensure the work area is safe, with proper traffic control if necessary, and that all personnel are equipped with appropriate personal protective equipment (PPE).
EPCOM recommends that all its pole line hardware components are installed by professionals following established industry best practices and local utility standards.
Ensuring Longevity: Maintenance Tips
Regular inspection and maintenance are vital to extending the service life of pole line hardware and preventing unexpected failures. A proactive maintenance program can identify potential issues before they escalate into major problems.
- Routine Visual Inspections: Conduct regular visual inspections of poles, conductors, and all accessible hardware. Look for signs of corrosion, wear, damage (e.g., from weather or vandalism), loose components, or leaning poles. Drones are increasingly used for safer and more efficient inspections.
- Corrosion Monitoring and Mitigation: Pay close attention to steel components for signs of rust or deterioration of galvanized coatings. Apply appropriate anti-corrosion treatments if necessary. This is particularly important for durable pole line hardware in coastal or industrial environments.
- Checking Connections: Periodically verify the tightness of critical bolted connections, especially in areas prone to vibration. Thermal imaging can be used to detect hot spots at electrical connections, indicating high resistance and potential failure.
- Insulator Cleaning and Inspection: In areas with high pollution or salt spray, insulators may need periodic cleaning to prevent flashovers. Inspect insulators for cracks, chips, or signs of tracking.
- Guy Wire Tension Checks: Verify that stay wires maintain proper tension. Adjust as necessary to compensate for creep or environmental effects. Ensure that guy guards are in place and visible.
- Vegetation Management: Keep trees and other vegetation clear of lines and hardware to prevent physical damage and reduce fire hazards.
- Hardware Replacement Schedule: Based on inspections and expected lifespan, plan for the timely replacement of aging or deteriorating pole line hardware before failure occurs.
- Record Keeping: Maintain detailed records of inspections, maintenance activities, and component replacements. This data can help in identifying trends, predicting future maintenance needs, and optimizing asset management strategies.
By investing in quality pole line hardware from suppliers like EPCOM and implementing robust installation and maintenance programs, utilities can significantly enhance the reliability and longevity of their overhead networks.
Innovations and Future Trends
The field of pole line hardware is continuously evolving, driven by the need for greater reliability, easier installation, longer service life, and adaptation to new technologies like smart grids and advanced communication networks. Several trends and innovations are shaping the future of overhead pole line hardware.
Material Science Advancements in Pole Line Hardware
New materials and improvements in existing ones are leading to more durable and efficient pole line hardware components.
- Composite Materials: Fiber-reinforced polymers (FRPs) and other composite materials are being used for crossarms, poles, and even some hardware components. These materials offer high strength-to-weight ratios, excellent corrosion resistance, and good insulation properties.
- Advanced Coatings: Innovations in galvanizing and other protective coatings are extending the lifespan of steel hardware, even in highly corrosive environments. Polymer coatings and duplex systems (e.g., galvanizing plus paint/powder coat) offer enhanced protection.
- Improved Insulator Materials: While porcelain and glass remain common, polymeric (silicone rubber, EPDM) insulators are gaining popularity due to their light weight, resistance to vandalism, hydrophobic properties (which resist surface contamination), and better performance in certain polluted environments.
- Higher Strength Alloys: Development of higher strength steel and aluminum alloys allows for more compact or lighter hardware designs without compromising mechanical performance.
Smart Features and Monitoring for Pole Line Hardware Systems
The integration of sensing and communication technologies is transforming pole line infrastructure into smarter, more responsive systems.
- Sensor-Embedded Hardware: Components are being developed with embedded sensors to monitor conditions such as stress, temperature, inclination (for poles), or insulator leakage current. This data can provide early warnings of potential failures.
- Real-Time Monitoring: Wireless communication allows for real-time transmission of data from sensors on pole line hardware to control centers, enabling utilities to proactively manage their assets and respond quickly to issues.
- Fault Detection and Localization: Advanced hardware and software systems can help pinpoint the location of faults more accurately and rapidly, reducing outage durations.
- Dynamic Line Rating (DLR): By monitoring conductor temperature and environmental conditions, DLR systems can allow utilities to safely operate lines closer to their thermal limits, increasing transmission capacity without building new lines. This requires accurate data from various pole line hardware mounted sensors.
Designing Pole Line Hardware for Resilience and Sustainability
There is an increasing focus on making overhead lines more resilient to extreme weather events and on improving the environmental footprint of pole line hardware.
- Hardened Designs: Hardware is being designed to withstand higher wind loads, greater ice accumulation, and increased wildfire risk, reflecting the impacts of climate change. This includes stronger poles, more robust crossarms, and more secure conductor attachments.
- Environmentally Friendly Materials: Efforts are being made to use materials that are more sustainable, either through recycled content, reduced toxicity, or easier recyclability at the end of their service life. Wood preservatives with lower environmental impact are also a focus.
- Wildlife Protection: Enhanced designs for wildlife protectors and modified construction practices aim to minimize bird electrocutions and collisions, supporting biodiversity.
- Ease of Installation and Maintenance: Innovations that make pole line hardware installation and maintenance safer, faster, and less labor-intensive are constantly being sought. This can include modular designs, pre-assembled components, and tools that reduce physical strain on lineworkers.
EPCOM is committed to staying at the forefront of these innovations, ensuring that our customers benefit from the latest advancements in pole line hardware technology. We believe that the future of power and communication relies on smarter, stronger, and more sustainable infrastructure.
Component Category | Specific Examples from EPCOM | Primary Function | Key Material Considerations |
---|---|---|---|
Anchoring & Guying | Stay Wire, Stay Rod, Stay Plate, Stay Thimble | Stabilize poles against lateral forces, ensure structural integrity. | High tensile strength steel, Hot-dip galvanization for corrosion resistance. |
Insulation | Stay Insulator, Pin Insulators, Suspension Insulators | Prevent electrical current flow to pole/ground, ensure safety, minimize power loss. | Porcelain, Polymer (Silicone Rubber, EPDM), Glass. High dielectric strength, mechanical strength. |
Conductor Support | Crossarms, Suspension Clamps, Dead-end Clamps, Pole Top Pins | Physically hold conductors in place, manage conductor tension. | Steel, Aluminum Alloy, Ductile Iron, Wood, Composites. Strength, corrosion resistance, conductor compatibility. |
Fastening & Joining | Machine Bolts, Eye Nuts, Square Washers, Parallel Groove Connectors | Assemble and secure hardware components, join conductor sections. | Hot-dip galvanized steel, Stainless Steel, Bronze. Strength, durability, corrosion resistance. |
Protection & Safety | Grounding Wire, Ground Rods, Guy Guards, Wildlife Protectors | Ensure system grounding, protect equipment and personnel, prevent wildlife interaction. | Copper, Copper-clad steel, Galvanized Steel, UV-stabilized polymers. Conductivity, durability. |
Comprehensive Guide to Pole Line Hardware Specifications
Understanding the specifications of pole line hardware is crucial for engineers, procurement specialists, and field personnel. These specifications ensure that the selected components are appropriate for the application, compatible with other parts of the system, and capable of withstanding the expected mechanical and electrical loads, as well as environmental conditions. Detailed specifications for pole line hardware usually cover aspects like material composition, mechanical strength, dimensional tolerances, coating requirements, and applicable industry standards.
Material Specifications for Pole Line Hardware
The choice of material is fundamental to the performance and longevity of any pole line hardware component.
- Steel Components: Often specified by ASTM standards (e.g., ASTM A36 for structural steel, ASTM A153 for hot-dip galvanization). Key properties include tensile strength, yield strength, and ductility. Forged steel is often preferred for high-strength applications due to its refined grain structure.
- Iron Components: Ductile iron (e.g., per ASTM A536) is commonly used for items like anchor rods, clamps, and fittings due to its good castability, strength, and wear resistance. Malleable iron was historically used but has largely been replaced by ductile iron.
- Aluminum Components: Aluminum alloys (e.g., 6061-T6 or 356.0-T6) are used for clamps and connectors, especially when connecting to aluminum conductors, to minimize galvanic corrosion. Specifications will cover alloy composition and temper.
- Bronze Components: Bronze alloys are used for certain types_of_connectors due to their excellent conductivity and corrosion resistance, especially in harsh environments or for connecting dissimilar metals.
- Insulating Materials: Porcelain specifications often refer to ANSI C29 standards, covering electrical and mechanical properties. Polymer insulators will have specifications related to their housing material (e.g., silicone rubber), core rod (e.g., FRP), and end fitting materials.
- Galvanization: For steel pole line hardware, the thickness and adherence of the hot-dip galvanized coating (usually specified in ounces per square foot or microns) are critical for corrosion protection. Standards like ASTM A123 (for structural steel products) and ASTM A153 (for hardware) are key.
Mechanical Strength Requirements in Pole Line Hardware Solutions
All load-bearing pole line hardware must meet specific mechanical strength ratings. These are often expressed as:
- Ultimate Tensile Strength (UTS): The maximum stress a component can withstand before fracturing.
- Working Load Limit (WLL) or Safe Working Load (SWL): The maximum load that can be applied to a component during normal service, usually a fraction of the UTS to provide a factor of safety.
- Cantilever Strength: For components like insulators and crossarms, this measures their ability to withstand bending forces.
- Impact Resistance: Particularly important for components in areas prone to vandalism or accidental impact.
Manufacturers like EPCOM provide detailed strength ratings for their products, which must be carefully matched to the calculated loads of the overhead line design. For example, the EPCOM Stay Rod series will have specific UTS ratings based on diameter and material.
Dimensional Tolerances and Compatibility
Precise dimensions and tolerances are essential for the proper fit and assembly of pole line hardware.
- Pole Fit: Hardware designed for specific pole diameters (e.g., pole bands, crossarm gains) must have accurate dimensions.
- Conductor Range: Clamps and connectors are specified for a certain range of conductor diameters. Using them outside this range can lead to poor connections or conductor damage.
- Thread Standards: Bolts, nuts, and threaded portions of rods must adhere to standard thread profiles and sizes (e.g., ANSI/ASME B1.1 for Unified Inch Screw Threads).
- Hole Spacing: For components like crossarms and mounting brackets, the spacing and diameter of bolt holes are critical for interchangeability and correct assembly. NEMA standards often define standard hole spacings.
Reviewing manufacturer datasheets, such as those provided by EPCOM for its Stay Thimble or Stay Plate, is crucial for verifying these dimensional specifications.
Industry Standards and Certifications
Compliance with recognized industry standards provides assurance of quality, safety, and interoperability for pole line hardware.
- ANSI (American National Standards Institute): Publishes numerous standards relevant to electrical equipment, including insulators (ANSI C29 series) and pole line hardware.
- IEEE (Institute of Electrical and Electronics Engineers): Develops standards related to power engineering, including guides for overhead line construction and component testing (e.g., IEEE Standard 1070 for guy anchors).
- ASTM International (American Society for Testing and Materials): Provides material specifications and test methods crucial for ensuring the quality of metals, coatings, and other materials used in pole line hardware.
- IEC (International Electrotechnical Commission): Develops international standards for electrical, electronic, and related technologies, which are widely adopted globally.
- RUS (Rural Utilities Service): Part of the USDA, RUS publishes specifications and standards for equipment used in rural electrification projects financed by them. These are often very detailed and widely respected.
When selecting pole line hardware suppliers, inquiring about their adherence to and certification against these standards is a key part of the due diligence process. EPCOM is committed to providing products that meet or exceed applicable industry standards, ensuring reliability for your utility pole line hardware needs.
Understanding these specifications not only aids in selecting the right components but also in drafting accurate procurement documents and ensuring quality control throughout the supply chain and installation process. The intricacies of pole line hardware specifications highlight the engineering precision required for these seemingly simple components, which are nonetheless vital for the functioning of our critical infrastructure.
Conclusion: The Enduring Necessity of Quality Pole Line Hardware
Pole Line Hardware, in its myriad forms, remains an indispensable element of our modern world. It is the silent workhorse that supports the vast networks delivering essential electricity and communication services to homes, businesses, and industries. From the robust Stay Wire ensuring pole stability to the critical isolating function of the Stay Insulator, and the foundational support of Stay Rods coupled with Stay Thimbles and Stay Plates, each component plays a crucial role.
The increasing demands for uninterrupted power, higher data speeds, and resilient infrastructure in the face of environmental challenges underscore the need for high-quality pole line hardware. Innovations in materials, design, and smart technologies continue to enhance the performance and longevity of these components. However, the fundamental principles of robust design, quality manufacturing, correct installation, and diligent maintenance remain paramount.
EPCOM is dedicated to being a leading provider of durable pole line hardware, offering a comprehensive range of products designed to meet the stringent requirements of today’s utility and telecommunication industries. By choosing EPCOM, you are partnering with a company that prioritizes quality, reliability, and customer satisfaction, ensuring that your investment in overhead pole line hardware contributes to a safer, more efficient, and more connected future. As infrastructure continues to expand and modernize, the role of superior pole line hardware components will only grow in importance, and EPCOM is poised to meet that evolving need.